PVC is the insulation of choice for almost any cable we see around us in our day-to-day lives. Everything from mains cable through to leads on headphones and mobile phones are invariably PVC. In general, PVC is not a very commonly used cable for many temperature applications due to its limited operating range. Standard PVC is only suitable for use in the range -10 to +70°C. A high-temperature version more commonly used in this industry extends the upper limit to 105°C. There are still plenty of applications that fall within this range and if the application permits the use of PVC then it is the lowest cost option.
Pt100 Wiring Methods – 2, 3 or 4 wire?
The wiring of a Pt100 temperature sensor is different to other temperature sensors, in particular thermocouples. It is important to get the wiring of your sensor correct otherwise the measuring instrument may give an incorrect reading or no reading at all.
Conductor material
Cables used for connecting a Pt100 sensor usually have copper-based conductors. In our own sensors, we use plated copper; either tin, silver or nickel-plated depending on the temperature range required. It is however permissible to use plain copper.
For very high temperatures we use Nickel-based cables. Note that the resistance of Nickel is about 5 times that of copper and therefore you should always use a 3 or 4 wire connection system (see below).
The conductor size does not need to be very large. For example, there is no need to use power cable, instrument cable is sufficient. We usually use 7/0.2mm, 24AWG stranded conductors in our own sensors, even with cable lengths of many metres without issue. Of course, it is possible to use a large cable for very long cable lengths but this usually just adds unnecessary cost for shorter runs. For long cable runs, we recommend using a temperature transmitter instead.
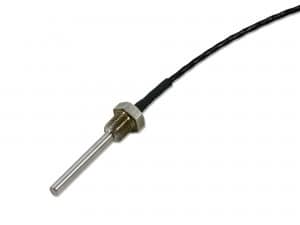
Pt100 sensor
calibration